
Concrete Slab & Exposed Aggregate Floors
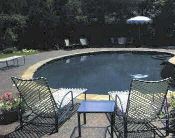

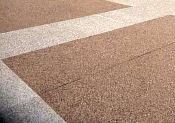
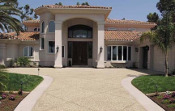
Penetrating type sealer: for a surface of very different absorption characteristics like this, the sealer choice is best if oriented to the lowest absorption part (the pebbles). It is easy to add another application of sealer if the higher absorption part (the concrete) needs it.
For a coating type sealer the absorption difference is not a concern.
Certain conditions that accelerate the drying process of freshly poured concrete (heat, wind, waterproof underlayment) can create two preventable conditions:
Surface (or deeper) shrinkage cracks and lower ultimate strength concrete
Both are preventable by using a "curing compound" that slows down the water evaporation process.
If your exposed aggregate has loose pebbles and/or "powdering" cement, then the best choice is a petroleum solvent based acrylic sealer. It will create a light gloss on the pebbles, no gloss on the concrete, and strengthen the concrete and it's bond to the pebbles.
Further "Items of Interest" for this surfacing, and all others, are at the bottom of this page.
Your Choices for Sealing
This surface has two very different absorption characteristics. The pebbles are much denser and lower absorption than the concrete. It is usually best to make the choice based on the pebbles so there is not to much gloss buildup on them.
Our suggestions to test are:- Penetrating petroleum solvent formulas with acrylic solids. These can be sprayed to finish nicely, but solids level might need to be adjusted if manufacturer allows dilution.
- Water based film forming that can flow out and self-level.
- Water based penetrating that is usually invisible when dry. However, test for sealer residue (usually white) on the pebbles.
- Click here to see What effects you can expect from each sealer type.
- Click here to see our suggested sealers, cleaners, and application tools.
Some questions you may not be thinking to ask right now that could become important:
. Was it sealed in the past? Does that matter?
. Will a new sealer be compatible with whatever was used before?
. What sealer will give the visual results you want?
. Will you also be able to have a sealer solve problem(s)? ( Answer: yes. Just know which to pick.)
Items of Interest
How to select a sealer
A sealer can do far more than just bead water and look pretty! To see what that is click here.
Important: If your project has had any sealer applied in the past, it must be evaluated differently. To see why, Click here!
Sealer "solids" levels?
A porous surface will require more gallons (more money) of a lower solids sealer than using a higher solids level sealer. That, plus different surfaces have different requirements. It is only a matter of which is best for your needs.
The more porous the surface, the more solids will be required to achieve the desired effects of gloss, strengthening, stopping efflorescence, etc.
The more porous the surface, generally the greater the need for the sealer to create a stronger surface.
An old sealer below the surface, even after stripping, will lower the absorption and porosity to some degree. Sometimes it is uneven below the surface and can create an uneven coloring effect with a color enhancing sealer applied later. Another reason to test first.
Do not believe yet that you have the type of surfacing you were told:
Colors fading?
Renew a glossy finish
Re: "penetrating sealers": do not apply thin layer upon thin layer. Apply a sufficient quantity to insure below surface penetration & bonding. A layer of sealer on top of another layer of sealer can result in poor bonding between layers and that can cause separation peeling that looks grayish.
Concerned about Doing It Yourself or what your contractor says?
If you are concerned about doing it yourself - consider that the satisfaction of a project is directly related to YOUR knowledge of what needs to be done and how. Who actually does the work is less important.
The goal for contractors is - NO CALL BACKS. A good contractor will understand the logic of not taking shortcuts.
©
The goal for contractors is - NO CALL BACKS. A good contractor will understand the logic of not taking shortcuts.